For any food business, be it a restaurant, cafe, or even a coffee shop, walk-in coolers, and freezers are imperative to running a successful business. Choosing the right flooring for this ever-important piece of equipment is crucial, as you can go down different paths of costs and maintenance, and even success and failure, depending on which flooring option you choose for your needs.
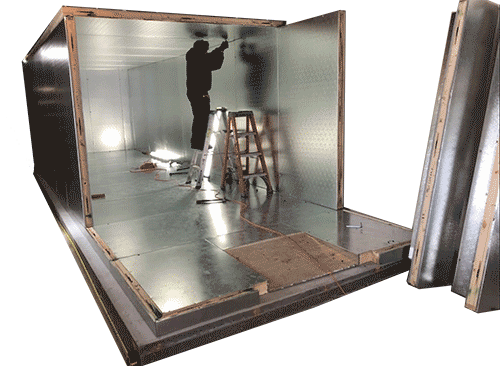
Walk-in coolers and freezers are responsible for storing the actual lifeblood of your business: the food! Because of this, the decision is not one to be taken lightly. It needs to be informed and calculated. For this reason, we’ve compiled a list of things to consider when contemplating the floor of your walk-in.
Floorless versus Insulated Floors
It may sound odd for a first-time buyer, but not every walk-in comes with a floor. This is one reason why it’s so important to make an informed decision. The only real reason to stay floorless is if temperature control is not a huge concern, which could make sense for a business such as a floral shop, which needs cold storage, but doesn’t necessarily need strict temperature control. If this is the case, adding sealers between the walls and floors can serve as enough insulation, so long as the walk-in is built upon a concrete floor.
With any other situation wherein temperature control is important, having an insulated floor is the only option, as floorless simply cannot provide effective cooling. Without it, cold air can escape easily and warm, humid air can enter willy-nilly. However, there are even more options to consider beyond floorless versus insulated…
What should I consider?
Choosing the right flooring depends heavily on what its intended use will be and the amount of foot traffic you expect it to get.
Foot traffic. This is extremely important. Depending on what’s being stored inside the walk-in and its level of daily use, foot traffic can range dramatically–it can be opened once or twice, or people could be going in and out of it every 5 minutes. This is one of the most important things to consider.
Location. A walk-in should always sit on a concrete slab whenever possible, as condensation is the driving factor in flooring damage. Concrete does a great job of limiting heat transfer which can help reduce wear and tear on the unit. If not, the condensation that can eventually form can seriously damage flooring and risks the entire building’s integrity.
Access. This goes back to how the walk-in will be used. Will line cooks simply be going in and out and hand-toting boxes, using carts that necessitate ramps? Does there need to be extra space or recession to allow for the entrance of rolling carts and racks? Thinking about the accessibility of the space can make this decision easier.
Moisture/humidity. If the walk-in will be built above a crawlspace, basement, or above another floor of a building, you must use insulated flooring. This is because it prevents condensation from forming–hot air rises, which means that heat will be circulating under the walk-in via whatever space is below it. With an insulated floor, you can avoid condensation build-up on the floors which can not only prevent structural damage but can prevent workers or guests from injuring themselves as well.
What are the types of flooring?
When consulting with a professional about getting the right flooring, it helps a ton to be familiar with the common flooring types, which include:
Aluminum panel flooring. This is the standard flooring that is made with similar materials that the walk-in itself is made. They are usually laid in panels with fixed foam placed between the panels. This is suitable for regular foot traffic, but cannot support things such as pallet jacks or very heavy carts.
Plywood underlay. This is aluminum panel flooring 2.0. It features, you guessed it, plywood underlay which helps reinforce the flooring and allows for slightly heavier things such as carts and racks.
Reinforced floors. These are the heavy-duty floors that can basically withstand anything. They feature plywood understands which are reinforced by metal grid supports. They can withstand huge amounts of weight, which means that very heavy things like beer kegs or manually operated pallet jacks are safe to use here.
Call us
Here at Tri-Point, we handle every aspect of the installation of any new walk-in cooler or freezer. We are on the job from ordering to full completion and would be more than happy to assist you in choosing the right flooring for your walk-in cooler or freezer. Start right here by giving us a call here at Tri-Point Refrigeration and we would be ecstatic in helping you in your walk-in freezer journey! We’re excited to help you along the way, and our professional technicians can help find the perfect spot for your walk-in. With good placement and regular servicing, we can keep your equipment running smoothly and healthily, while also extending the reach of your dollar.
For a direct line to any of our employees ready on the line to help you, please call…(512) 651-4565 for our Austin, Texas community (806) 686-0050 for our Lubbock, Texas community. Or check out our website at https://www.tripointrefrigeration.com