Oh no! Your walk-in is warm again, isn’t it? That is the worst! Sometimes you just can’t catch a break. In Texas’ unrelenting summer heat a warm walk-in is never good news. Well we’re going to go over ten things to check on your walk-in that could be the problem. Hint, 80% of the time it is not low on refrigerant. The information below is for educational purposes. If you attempt any diagnosis on your own based upon what is written here, you are responsible for your actions but you know that already, don’t you? This began as a short list of possible problems with short descriptions and morphed into thousands of words about what could be wrong with your cooler and what steps we take to solve the problem. Considering this, I broke this post up into multiple blog posts rather than overwhelm readers a five-thousand word blog post. They are useful words but too many might be less than helpful. We want to be helpful.
10 common reasons why your walk-in isn't working. Part 4
8. Compressor
The compressor is the heart of the system and if it has died it is game over for your walk-in refrigeration until it is replaced. There are a few things that can go wrong with a compressor. The most common are: The compressor can lock up (LRA) and not be able to move the valves anymore. The compressor could have open electrical windings inside meaning that there is a break internally electrically. It can also be grounded out meaning that something electrical inside has shorted to ground. The last major issue that happens to compressors is that the valves inside get weak and can’t move enough refrigerant anymore. The average walk-in at a restaurant is not repairable internally. They are welded shut and there is no way to get inside of the compressor to replace any parts. Manufacturers do not even offer replacement parts for the welded shut compressor. Diagnosing a compressor issue is compounded by the internal overload which will cause the compressor to appear that it has open windings when in fact it does not. We diagnose a compressor by eliminating other electrical and refrigerant issues and testing.
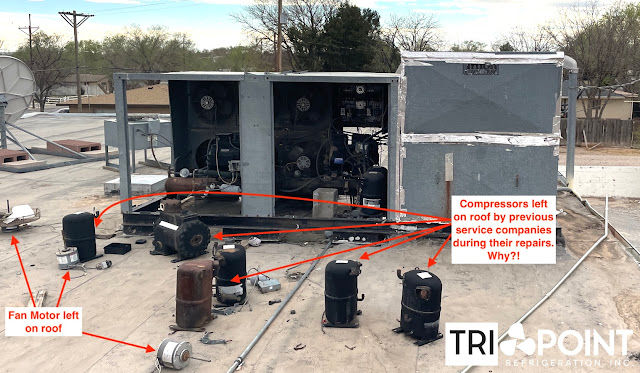
We first check the start components. We check to be sure the start and run capacitors have the appropriate microfarad rating then we check to see that the relay is not burned or locked up. We then disconnect the contacts to the compressor and check the terminals to be sure that they are not open and the contacts all show resistance on an ohmmeter. If there is no resistance between any contacts it means that it has a short. We also test between the terminals and the ground to see if it is shorting to the ground. If either of those situations happen then it is time for a new compressor.
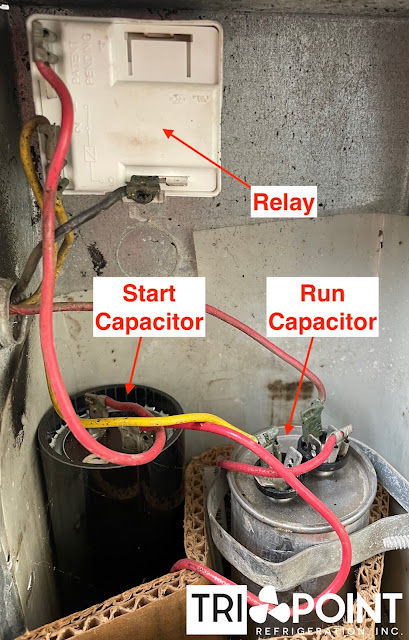
If we test the terminals on the compressor and find that the circuit is open we check to be sure that the internal overload has not tripped. The internal overload can trip if the compressor gets too hot so we will dump water on the compressor or even get a bag of ice to help cool it down. The internal core deep inside of the compressor often takes at least 15-30 minutes to get the internal OLP to close if that is the issue. If the overload closes, great. But, it doesn’t mean you have solved the problem. What caused the compressor to overheat like that? Often it isn’t even a compressor issue. It could be due to dirty coils overheating the system, too much refrigerant in the system or restrictions in the system that are causing high pressure. If after all of that you still have open windings it is time for a new compressor.
Weak valves can be diagnosed by attempting to pump down the system. We do this by having the compressor pump all of the refrigerant into the condenser. If the compressor is not able to pump the refrigerant into the condenser and hold it there we typically deduce that the compressor is no longer able to function at its designed pressures and needs to be replaced.
9. Solenoid coil or valve
The liquid solenoid valve is what allows refrigerant to flow. When the thermostat turns on the solenoid valve it opens and lets refrigerant pass through. As the refrigerant passes through it moves through the evaporator and raises the pressure of the refrigerant in the pipe on the way back to the compressor. The low pressure switch senses the pressure rise and turns on contactor which in turn turns on the condensing unit. Woah. Did you get all of that? If the solenoid valve is not opening, refrigerant can not flow and your walk-in will get warm. Two things can be wrong with the solenoid. There is also a really cool app from Danfoss that can detect magnetic fields which easily tells you if the coils are working or not.

The first thing to check is that the electromagnetic coil is activating. The electromagnetic coil is energized and pulls up the plunger allowing refrigerant to flow. If that electromagnet is not functioning anymore the solenoid valve will not work. We check to be sure voltage is being supplied to the coil. If power is getting to the coil we check for amp draw on the coil. If no amps are being pulled with power applied to the coil then the coil is bad and needs to be replaced. Another way to test the coil is to measure the resistance of the coil. So long as there is resistance it should be okay.
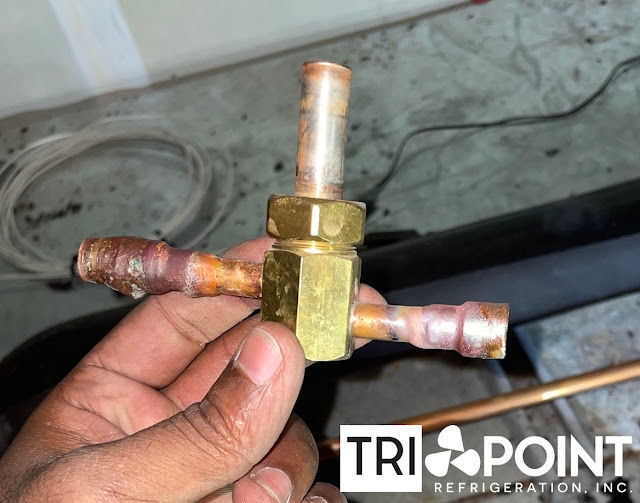
The second thing to check is if the solenoid valve is opening. Typically if everything is functioning you can hear the clunk of the solenoid opening followed by the hiss of refrigerant. But if your solenoid coil is dead how do you verify that the valve is opening? A donut shaped magnet is the answer. It does the same thing as the electromagnet. If the donut shaped magnet doesn’t open the valve something is wrong in the valve itself and it should be replaced.
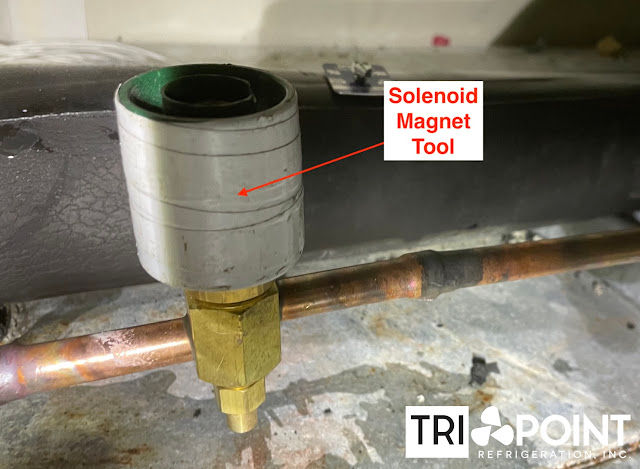
The solenoid valve on occasion may be found to not close anymore. It may appear to open and close but it may be stuck slightly open which causes it to act like the TXV and will inevitably cause liquid lines past the solenoid to freeze over. Sometimes this can be freed up by clubbing the valve with a wrench but it doesn’t guarantee that it will not happen again and the solution is generally to replace the solenoid valve.
We'll continue this series of 10 common reasons your walk-in isn't working next week when we talk about the TXVs and Klixons. Don't forget to check back in next week or add us to your RSS feed so you don't miss out. If you are having trouble with your refrigeration equipment in Austin, TX or in Lubbock Texas give us a call for service or new equipment. We are always happy to help! 512-651-4565 in Austin and 806-787-4985 in Lubbock, Texas Or Visit our website at https://www.tripointrefrigeration.com